Die sinking EDM (Electrical Discharge Machining), a cornerstone in modern manufacturing, is a fascinating story of technological evolution. It's more than just a process; it's a revolution in how we create complex shapes, intricate designs, and precise components.
In this article, we’ll explore:
- The basics of how die sinking EDM machines work
- The historical development of die sinking EDM and its impact on manufacturing
- The latest innovations and what the future might hold for this technology
Join us as we unpack the evolution of die sinking EDM, a remarkable technology that continues to shape the manufacturing industry and the exciting possibilities it holds for the future of precision manufacturing.

How Die Sinking EDM machines work
Die sinking EDM, also known as spark eroding or die sinking, operates on a novel principle: shaping materials with electrical sparks. Unlike traditional machining, it doesn't rely on cutting tools. Instead, it uses electrical discharges to mould materials, typically metals, into precise shapes.
Think of it like electrical sculpting for metal, shaping metal using sparks, but in a very controlled way.
Let’s break down this process:
Electrode and workpiece
The process involves two main parts, the electrode and a workpiece, both submerged in a dielectric fluid. The electrode, which is shaped exactly like the design you want, doesn’t actually touch the workpiece. Instead, it gets close enough to shape it without any physical contact.
Creating the spark
When the electrode is brought close to the workpiece, an intense electric field is generated. As the voltage increases, sparks jump across the gap. These sparks are the key to shaping the metal, chipping away tiny bits to create the desired form.
Controlled erosion
This isn’t random sparking; it’s very precise. The machine carefully controls these sparks to ensure precise erosion, only removing what’s needed from the workpiece. This method allows for complex shapes and fine details, something that’s impossible to achieve with conventional machining.
Cooling and flushing
The dielectric fluid plays a dual role – to keep things cool and clean. It cools the heated area and flushes away the tiny metal particles, keeping the shaping process neat and accurate.
Historical overview of die sinking EDM technology
Die Sinking EDM’s journey from a novel idea to a cornerstone in precision manufacturing is a tale of innovation and adaptation, dating back to the 1940s; but it wasn’t until the 1950s and 1960s that die sinking EDM really began taking shape.
Initially, it was a method to remove broken taps and drills from metal components, a small yet significant start; but it wasn’t until the 1970s and 1980s when the breakthroughs happened, swiftly advancing this technology. This period saw the introduction of refined control systems and better electrode materials, which improved precision and efficiency. Soon, manufacturers saw the potential of die sinking EDM beyond just removing broken tools.
As the technology matured, its applications expanded. By the 1990s, die sinking EDM had become a preferred method for creating complex moulds, aerospace components, and intricate medical devices. Its ability to handle hard materials and intricate designs made it a go-to solution for challenging manufacturing tasks that other machines simply weren’t capable of doing.
And then die sinking EDM entered the digital era with computer-controlled EDM machines further enhancing precision and allowing for ever more complex designs..
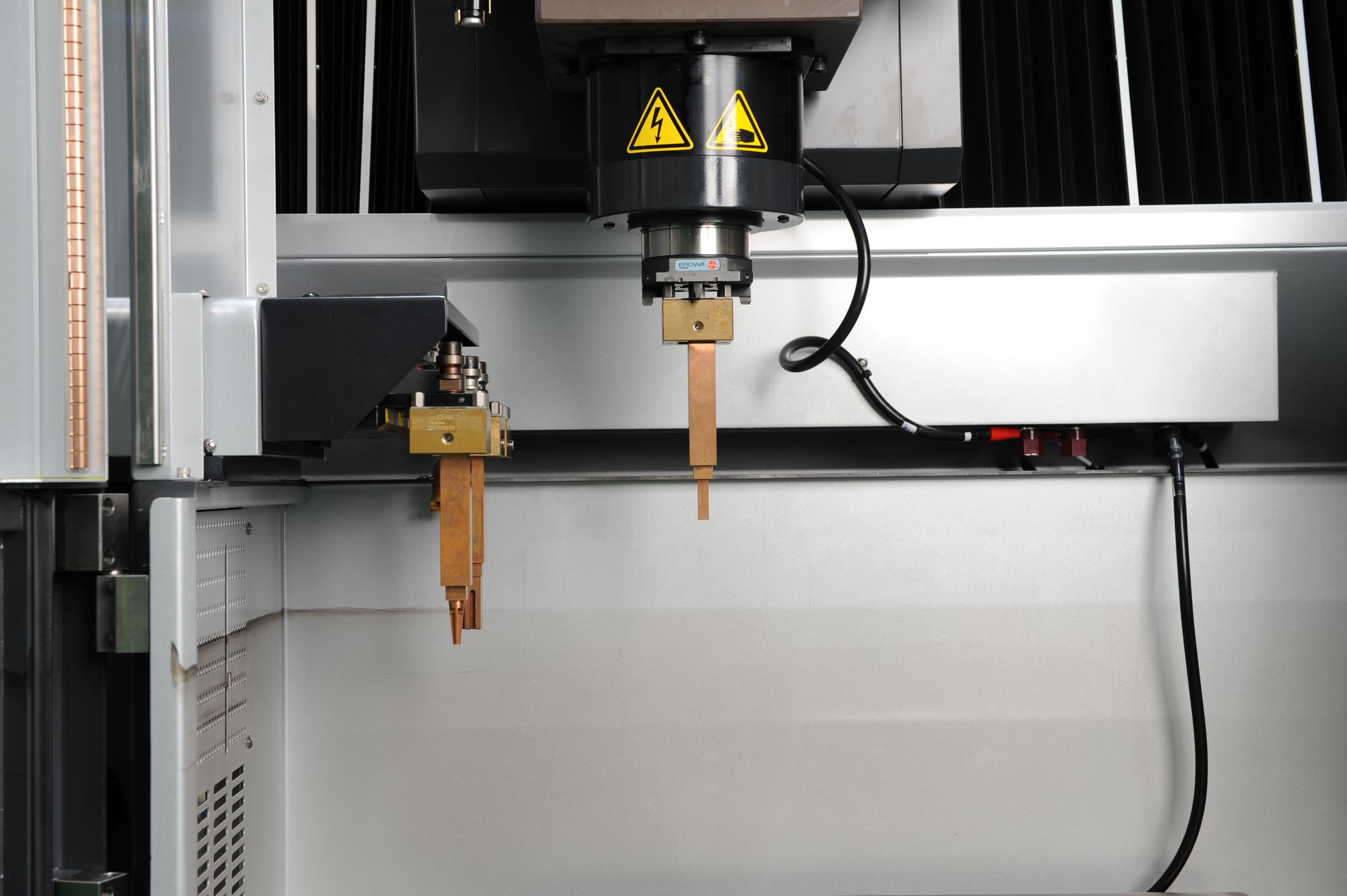
Current state of die sinking EDM technology
Today, die sinking EDM technology is an essential tool in modern manufacturing. Its current iteration reflects years of refinement, technological advancements and practical applications.
Modern die sinking EDM machines are equipped with highly sophisticated control systems. These systems enhance precision, allowing for the creation of complex and intricate designs with a higher degree of accuracy, critical in fields like aerospace and medical device manufacturing.
One of the standout features of today's die sinking EDM is its ability to work with a wide range of materials. Whether it's hard metals like titanium or delicate alloys, the technology handles them with ease, opening up a world of possibilities in various industries.
Finally, the integration of computer-aided design (CAD) and computer-aided manufacturing (CAM) systems has been a game-changer, significantly streamlining the production process. This allows for seamless transitions from design phase to actual manufacturing, minimising errors and optimising production timelines.
Innovations and technological advancements in die sinking EDM
Die sinking EDM technology isn't just holding steady; it's charging forward with impressive innovations and technological advancements. These developments are not only enhancing its capabilities, but are also setting new standards in precision manufacturing.
A few notable innovations of recent years include:
- Ultra-precision machining: This means even finer details and higher accuracy, making it suitable for applications where even a micron's difference matters.
- Automated and intelligent systems: Machines now come with better predictive maintenance capabilities and automated process adjustments, making them more efficient and user-friendly, enhancing productivity and reducing downtime.
- Improved energy efficiency: This not only reduces operational costs but also aligns with global sustainability goals, making it a more environmentally friendly option.
- Advanced electrode materials: The development of new electrode materials has expanded the capabilities of die sinking EDM, offering better performance, longer life, and improved end-product quality.
Future trends and predictions in die sinking EDM technology
Now for the best bit: the future of die sinking EDM technology is poised for exciting developments.
Integration with advanced robotics
We’re anticipating a future with a greater integration of die sinking EDM with advanced robotics. A combination that could lead to even more precise and efficient manufacturing processes, especially in complex and labour-intensive tasks.
AI and machine learning enhancements
Artificial intelligence (AI) and machine learning are changing the world, and their impact is likely to once again revolutionise die sinking EDM by optimising machining parameters for enhanced efficiency and accuracy. Predictive analytics could also play a role in machine maintenance and process improvement.
Nano-technology applications
As nano-technology continues to advance, die sinking EDM could play a key role in the manufacturing of nano-scale components, something that would be significant in sectors like electronics and micro-mechanics.
Transform your manufacturing capabilities with Sodick EU
The evolution of die sinking EDM technology is more than just a technological advancement redefining manufacturing boundaries, it's a gateway to new possibilities in precision manufacturing. So, isn't it time to consider what it could do for your business?
Don’t just keep up with the industry, lead it. Reach out to us at Sodick EU today and let's chat about turning these incredible advancements into your competitive edge. Your future in precision manufacturing awaits!